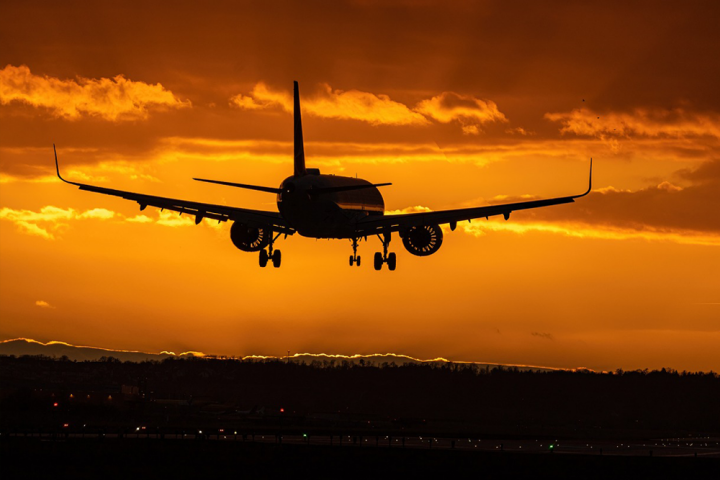
Plein gaz pour les composites
Plein gaz pour les composites
Perçue comme étant à la pointe de la modernité, l’utilisation des matériaux composites n’est pourtant pas une véritable nouveauté dans le monde de l’aviation. L’aéronautique fait même figure de pionnier puisqu’elle est l’une des premières industries à les avoir utilisés en masse et ce, malgré leur coût supérieur aux métaux qu’ils remplacent. Depuis les premières « machines volantes » créées par les frères Wright ou Clément Ader de notre côté de l’océan Atlantique, les avionneurs savent que le poids est un facteur déterminant pour bien faire voler un avion. C’était tout du moins vrai au temps des « faucheurs de marguerites », cela l’est moins maintenant où la puissance des moteurs est telle, qu’ils pourraient sans problème faire décoller des avions bien plus lourds. Aujourd’hui, cette quête de légèreté a d’autres enjeux. D’ordre économique car plus un avion est léger, moins il consomme. Et surtout d’ordre écologique car une moindre consommation génère moins de gaz à effet de serre.
Un moteur d’une puissance de 12cv, quelques planches de bois et de la toile de coton, une masse de 272kg… En 1903, suite à l’exploit des frères Wright, on était bien loin que avion passerait le mur du son moins de 5 décennies plus tard… |
Les polymères font le poids
Les matériaux composites se nomment ainsi car ils sont composés de différents éléments : une fibre (de verre ou de carbone par exemple) et une matrice. Une résine plastique vient coller et maintenir entre-elles les fibres et ainsi assurer la cohésion du matériau et le transfert des charges mécaniques entre les fibres. Ces matériaux ont fait leur apparition dans le monde aérien dès les années 1930 où une combinaison de fibres de verre et de résine était alors utilisée pour renforcer les hélices. Si ces dernières étaient plus solides, ce nouveau matériau n’était pas vraiment plus léger que le bois… Il faudra attendre les années 1970 pour voir l’apparition de nouveaux composites le plus souvent à base de carbone et de résine époxy.
![]() Les matériaux composites à base de résines polymères ont mis les avions à la diète. Plus légers, ils consomment nettement moins de carburant. Ici, la pose d’un panneau composite sur un inverseur de poussée. |
Ces matériaux hi tech s’annonçaient hauts en promesses tant ils sont légers certes, mais également très résistants notamment à la fatigue, insensibles à la corrosion et souvent aux agressions chimiques. De plus, étant moulés et non pas emboutis comme le sont parfois les métaux, ils permettent des design plus ambitieux pour faire face aux contraintes physiques que réclame le vol de ces mastodontes des airs. |
Seul bémol, leur mise en œuvre n’était alors pas aisée. Le moulage était fastidieux et requérait un grand nombre d’opérations manuelles. Quant aux temps de chauffe idéal pour bien les faire durcir, il relevait de techniques empiriques. Bref, le matériau était prometteur mais il fallait encore l’apprivoiser. A force d’opiniâtreté, les ingénieurs ont réussi à mieux les maîtriser et à les rendre conformes aux sévères normes aériennes. Aujourd’hui ils représentent 50% de la masse de certains gros porteurs. Ces 50% symboliques ont été atteint en premier par Boeing sur son 787 qui a reçu sa certification, comprendre son permis de voler, en 2011. Un exploit, alors que son concurrent de l’époque, le fameux Airbus A380, en contenait à peine 25%. Soucieux de prendre sa revanche, le constructeur européen présentait quelques années après son A350 qui se payait le luxe de franchir la barre des 50%. Sur ces avions, la carlingue, une partie des ailes et des ailerons ainsi que la queue sont composés intégralement de panneaux de fibres de carbone et de résine époxy. Quels progrès en à peine 50 ans quand on sait que le Boeing 747, la star de l’époque défrayait la chronique pour sa conception en alliage d’aluminium…
Des composites du nez à la queue
Si la chasse au poids en est la raison essentielle, les avionneurs s’intéressent également aux composites pour leurs autres qualités moins connues. Leur rigidité par exemple, est incomparable pour fabriquer des pièces de grandes tailles comme les éléments des ailes.
Leur procédé de fabrication par moulage permet également de réduire le nombre de pièces assemblées par vissage ou rivetage qu’il faut surveiller de très près et remplacer au moindre jeu. |
![]() Légers mais pas que… les composites sont également moulables à souhait ce qui permet de fabriquer des pièce d’un seul tenant là où il en aurait fallu plusieurs pour les métaux. |
Les parties mobiles de la queue et des ailerons sont conçues à partir du même matériau mais sous une forme de sandwich, un type de fabrication qui permet aux plaques de composites de mieux résister aux mouvements de torsion.
Elles sont constituées d’une âme en nid d’abeilles (une structure qui minimise la quantité de matériau utilisé pour une résistance maximale) en kevlar®, une fibre aramide, prise en sandwich entre deux couches en composite de fibres de carbone. C’est la même technique qui est utilisée pour le radome, le bout convexe de la pointe avant d'un avion.
Vu de l’extérieur, il s’agit d’un simple « embout » dont on imagine qu’il participe uniquement à l’aérodynamisme des avions. Mais pas seulement car derrière ce « capot » se cache le radar (notamment le très important radar météo capable de détecter les gros nuages). Or, pour être efficace, un radar doit pouvoir laisser passer les ondes électromagnétiques dans un sens et dans l’autre. Cela, tous les polymères savent très bien le faire… Sauf qu’un radome est très exposé aux impacts notamment aviaires. La fabrication en nid d’abeille les rend quasi invulnérables.
Dans la plupart des cas, ils sont enrichis de fils de cuivre pour dissiper les éventuels coups de foudre.
![]() Les matériaux composites utilisés pour fabriquer l’Airbus A350 représentent plus de 50% de sa masse. Une première dans l’histoire de l’aviation. |
Les composites se plient à toutes les exigences
Les zones qui relient les ailes à la carlingue sont constituées d’un composite de fibres de verre, particulièrement réputé pour sa robustesse. Seuls les bords d’attaque des ailes et les supports moteurs restent en métal : de l’aluminium pour les premiers et de l’acier voire du titane pour le second qui demeurent des matériaux de premier plan pour leur résistance aux impacts. Pour combien de temps encore ? Airbus renforce désormais une partie des ailes de son A320 avec de la fibre d’aramide, une fibre qui résiste à peu près à tout ! Preuve s’il en est de la maturité des matériaux composites, Boeing équipera son futur 777x d’ailes repliables en composite. Un choix osé mais qui a été certifié. Il faut dire qu’avec une envergure de 72 m, ce géant des air risquait de toucher les autres avions aux points de stationnement. Ces ailes se replieront au sol et lui feront gagner 7 m, tout en restant parfaitement stables en vol. Son système de charnières en métal et ses ailes en composite sont l’alliance parfaite de ce que chaque matériau sait faire de mieux.
![]() Boeing a osé le pari d’une aile repliable pour son 777. Un défi relevé avec succès par la subtile association des composites et des métaux. |
Festival du film pour les polymères
Les matériaux composites ont tout de même quelques inconvénients, notamment leur peu de capacité à conduire l’électricité et à l’évacuer en cas de foudroiement. Pour y remédier, une poutre de cuivre est le plus souvent insérée dans le fuselage.
![]() Pour dissiper l’électricité en cas de foudroiement, certains avions peuvent se « vêtir » d’un film polymère adhésif intégrant des fils de cuivre. |
Chez Solvay, on a même conçu un film polymère adhésif dit de surface qui peut intégrer un très fin maillage de fils de cuivre pour dissiper l’électricité. |
Pour rester dans l’univers des films, la Lufthansa a conçu en collaboration avec BASF, un film en polymère qui s’inspire de la peau du requin. A l’instar de la peau de ce poisson, bien connu pour ses capacités hydrodynamiques, il est constitué de millions de nervures en forme de prisme, chacune de 50 microns de profondeur (0.005 cm). Cette texture nervurée réduit le frottement de l’air sur la carlingue, et donc la traînée. 950 m2 de film appliqué sur un avion permet d’économiser 400 tonnes de kérosène et 1.200 tonnes de dioxyde de carbone par an. Si la flotte mondiale d'avions long-courriers était équipée de ce revêtement, ce sont près de cinq millions de tonnes de carburant qui seraient économisées chaque année.
Les plastiques en ont sous le capot
Dans certaines pièces de moteur soumis aux échanges gazeux, ce sont les polyimides thermoplastiques (TPI) et plus particulièrement le Polyétherimide (PEI) qui sont principalement utilisés. Mis en œuvre par injection, ce dernier plus léger que les métaux comme l’aluminium qu’il remplace, est capable de prouesses grâce à sa forte résistance aux températures élevées (au-delà de 150 °C), aux agressions chimiques, à l’hydrolyse et aux frottements.
Cette famille de polymères est compatible avec les températures élevées. A noter que l’on trouve également d’autres matières thermoplastiques haute performance, comme les polyaryletherketones(PAEK), et plus particulièrement le PolyEtherEtherKetone (PEEK), dans des graisseurs de trains d’atterrissage, mais cette fois-ci pour des raisons de poids, car il résiste aussi bien à la pression que le métal, tout en étant plus léger. |
![]() Les polymères haute performance comme le PEEK ont fait leur apparition dans de nombreux endroits comme les réacteurs. Leurs atouts : ils résistent à tout et surtout aux fortes chaleurs. |
Les polymères à base d‘époxy sont quant à eux utilisés dans des zones à l’avant des réacteurs pour réduire la consommation de carburant. Ici, ce n’est pas une masse plus faible qui est recherchée mais l‘abradabilité du matériau. Un revêtement est abradable lorsque, mis en contact avec un corps mobile, il s’use préférentiellement à ce corps mobile. Dans les réacteurs, on les trouve sur des joints de turbine. Pour comprendre, il faut savoir qu’en réduisant au minimum le jeu, entre les pièces mobiles (comme les pales) et leur carter, on améliore les performances aérodynamiques eu moteur et par conséquent son rendement. En cas de frottement, c’est donc le joint abradable qui sera creusé sans perte d’efficacité significative des pales. A noter qu’il est aujourd’hui question de placer de nouvelles pièces imprimées en 3D de ces polymères près des soufflantes pour atténuer le bruit de moteur. Ce polymère peut en effet être transformé par fabrication additive en métamatériau de type mico-échaffaudage (matériau architecturé à microstructure poreuse) présentant des qualités d’absorption acoustique de très haut niveau.
Grâce à l’utilisation de différents polymères comme le PEEK ou encore le composite carbone/epoxy pour les pâles, le moteur LEAP, développé par CFM et qui équipe environ 90 % des avions moyen courrier monocouloirs vendus dans le monde, a perdu plus de 450 kg par rapport à la génération précédente qui pesait près de 2 500 kg. Si ces chiffres sont conséquents, la véritable prouesse est d’avoir permis un gain de consommation de l’ordre de 30%.
![]() Grâce aux polymères, les dernières générations de moteurs comme le LEAP ont perdu 20% de leur masse par rapport aux générations précédentes. |
Aménagements intérieurs : les plastiques montent au feu
Coffres à bagages, revêtements de siège, chariots de service, cloisons, parois … les polymères occupent une place prépondérante dans l’habitacle des avions. L’éventail des polymères y est large, du polyamide autrement connu sous le nom de Nylon®, au polycarbonate ou encore au polyétherimides (PEI), voire aux traditionnels composites fibres de verre/époxy. Comme dans l’automobile, ces matériaux sont choisis prioritairement pour leur faible masse et leur propension à prendre toutes les formes. Sauf que dans le monde aérien, les normes de sécurité sont encore plus draconiennes notamment pour tout ce qui a trait à la résistance au feu. Ainsi, pour passer sous les fourches caudines des différents organismes certificateurs, les matériaux doivent avoir une excellente tenue au feu. C’est le cas du PVC qui vient isoler les câbles. Les polyetherimides (PEI) résistent aussi très bien à la chaleur et on les retrouve logiquement dans des pièces de tailles importantes comme les cloisons et autres parois. Pour les pièces plus petites, comme les systèmes de fixation, on préfère les polyamides additivés avec des retardateurs de flammes. Quant aux coffres, ils sont en composite de fibres de verre et d’époxy, un matériau indestructible, idéal pour des objets actionnés des milliers de fois au cours de leur vie.
![]() L’aménagement des cabines est aujourd’hui un facteur de différenciation très important pour les compagnies aériennes. Si les polymères sont présents pour leur faible poids, ils sont aussi capables, de par leur design et leur texture, de se montrer sous leurs plus beaux atouts. |
Cet ensemble de détails quasi insignifiants fait toute la différence… Ainsi le PEI peut également être enrichi de fibres de carbone pour le rendre encore plus résistant. Il va venir remplacer l’aluminium jusqu’alors utilisé dans les accoudoirs, les repose-pieds, les châssis de cafetière et les bras des tablettes. Au final, quelques dizaines de kg et autant de CO2 en moins. Ou autant plus de fret en plus…
Les plastiques dans un fauteuil
Si la structure des sièges est encore majoritairement en métal, le plus souvent de l’aluminium ou du titane, le reste est constitué de différents polymères comme le polycarbonate présent dans les accoudoirs ou habillages de sièges par exemple. Ici aussi, les fabricants cherchent encore à les alléger tout en respectant les normes de sécurité. Ce défi audacieux a été relevé une jeune entreprise française qui a développé un siège dont l’armature est faite de titane mais également de fibres de carbone. Il ne pèse que 4 kg contre 10 pour un siège traditionnel. Une réelle innovation puisqu’il s’agit là du premier siège en fibres de carbone certifié par les autorités aériennes. Depuis peu, ce siège est entré au catalogue de l’Airbus a320 et du Boeing 737.
![]() Les polymères sont présents dans les sièges depuis longtemps. Si l’armature est restée longtemps en métal, il existe aujourd’hui des modèles toujours plus légers qui intègrent des composites |
Enfin, les fibres végétales, comme celles de lin par exemple, pourraient dans un futur proche être utilisées pour concevoir les trolleys par exemple. Outre leur côté écologique, elles absorbent très bien les vibrations et le son comparé à leurs cousines en carbone et même aux métaux. Des qualités indéniables pour le confort des passagers et celui du personnel volant…